If you’ve ever wondered how metal labels withstand daily wear and tear in harsh environments—from factory floors to medical equipment—you’re not alone. Scratch-resistant metal labels are a critical component in industries where durability, legibility, and professionalism matter. But what exactly makes these labels so tough? Let’s break down the science, materials, and manufacturing magic behind scratch-resistant metal labels and why they’re a smart investment for businesses.
Why Scratch Resistance Matters for Metal Labels
Metal labels aren’t just fancy nameplates—they’re workhorses. Think about the environments they endure: chemicals, UV exposure, abrasion, and temperature swings. A scratched or faded label can lead to miscommunication, safety risks, or even compliance issues. For example, in aerospace or automotive manufacturing, a damaged part label could cause costly delays. Scratch resistance ensures these labels stay readable and intact for years, even in extreme conditions.
This is where the keyword “metal label” shines. Unlike plastic or paper alternatives, metal labels leverage advanced materials and coatings to achieve unmatched durability. But it’s not just about the metal itself—it’s the combination of science and engineering that creates a truly scratch-resistant product.
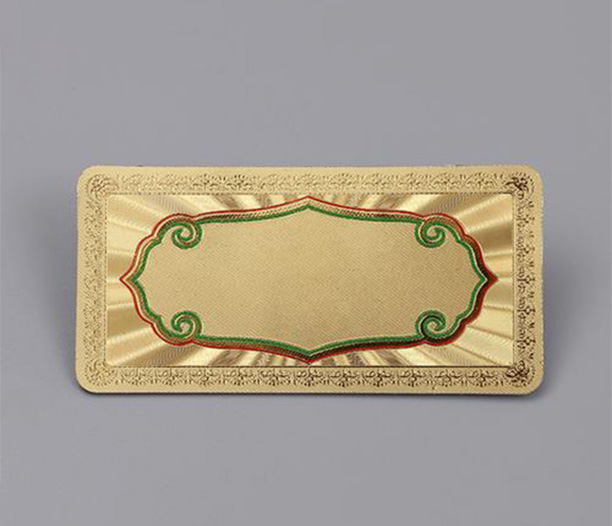
The Role of Material Science in Metal Label Durability
Not all metals are created equal. The most common materials used for scratch-resistant labels include:
- Anodized AluminumAluminum is lightweight and corrosion-resistant, but anodizing takes it to the next level. This electrochemical process thickens the metal’s natural oxide layer, creating a hard, non-conductive surface. Anodized aluminum labels can withstand scratches because the coating is integrated into the metal itself—not just painted on. Bonus: You can dye the oxide layer for vibrant, fade-resistant colors.
- Stainless SteelStainless steel’s chromium content forms a passive layer that resists rust and scratches. For extra protection, manufacturers often add coatings like epoxy or ceramic. Stainless steel metal labels are ideal for medical devices or marine applications where hygiene and moisture resistance are non-negotiable.
- Brass and Copper AlloysThese metals are softer but prized for their aesthetic appeal. To boost scratch resistance, they’re often coated with clear lacquer or subjected to chemical treatments.
How Coatings and Finishes Supercharge Scratch Resistance
The metal itself is just the starting point. Modern coatings add superhero-level protection. Here’s how they work:
- Polymer Coatings (Epoxy, Polyurethane): These create a flexible yet hard barrier over the metal label. Epoxy, for instance, bonds tightly to the surface and can include additives like UV inhibitors.
- Ceramic Coatings: Used in high-heat environments, ceramic coatings are ultra-hard and chemically inert.
- Physical Vapor Deposition (PVD): This space-age technique vaporizes metals like titanium or zirconium and bonds them to the label’s surface. PVD coatings are thinner than a human hair but dramatically improve scratch and corrosion resistance.
The Manufacturing Process: Precision Meets Innovation
Creating a scratch-resistant metal label isn’t just slapping on a coating—it’s a carefully orchestrated process. Here’s a peek behind the scenes:
- Laser Etching or Chemical EngravingFirst, the label’s text or design is etched into the metal using lasers or acids. This ensures the markings won’t rub off, even if the coating wears down.
- Surface PreparationThe metal is cleaned and treated to remove impurities. For anodized aluminum, this involves immersing the metal in an acid bath to open its pores.
- Coating ApplicationDepending on the desired finish, the label might be dipped, sprayed, or placed in a vacuum chamber (for PVD). Curing with heat or UV light locks the coating in place.
- Quality TestingLabels undergo rigorous tests—like Taber abrasion tests or salt spray chambers—to simulate years of wear in hours.
Real-World Applications of Scratch-Resistant Metal Labels
Where are these indestructible labels used? Let’s highlight a few industries:
- Medical Equipment: Autoclaves and surgical tools require labels that survive repeated sterilization.
- Outdoor Machinery: Construction and agricultural equipment need UV-resistant metal labels that won’t fade in sunlight.
- Electronics: Durable labels on circuit boards or industrial servers prevent misidentification.
Pro Tip: Pair your metal label with the right adhesive! Even the toughest label fails if it’s glued on with a weak adhesive.
Future Trends: Smarter, Greener Metal Labels
Innovation never stops. Emerging trends include:
- Nano-Coatings: Invisible layers that repel scratches, water, and even bacteria.
- RFID Integration: Metal labels with embedded RFID chips for inventory tracking.
- Sustainable Materials: Recycled aluminum and eco-friendly coatings reduce environmental impact.
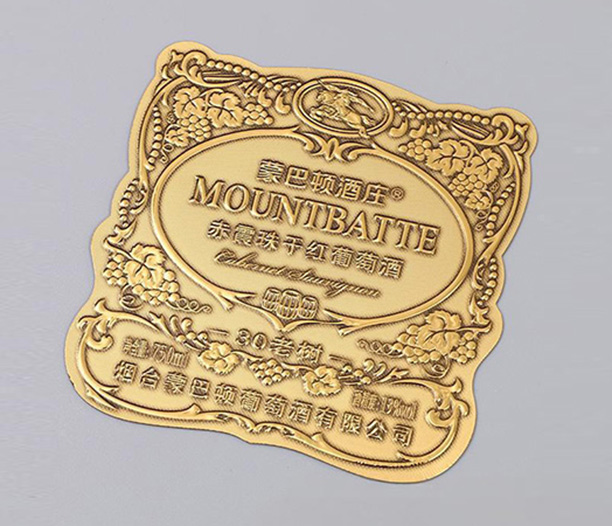
Choosing the Right Scratch-Resistant Metal Label
Not all metal labels are equal. Ask suppliers:
- What’s the base metal?
- Which coating technology do they use?
- Can they provide test results for abrasion or chemical resistance?
Final Thoughts
Scratch-resistant metal labels are a fusion of material science, cutting-edge engineering, and smart design. Whether you’re labeling a delicate lab instrument or a rugged oil rig component, investing in high-quality metal labels pays off in longevity and reliability. Next time you see a pristine metal label on a decades-old machine, you’ll know exactly what’s going on under the surface!
By understanding the science behind these tiny powerhouses, businesses can make informed choices—and avoid the “sticker shock” of replacing worn-out labels year after year.